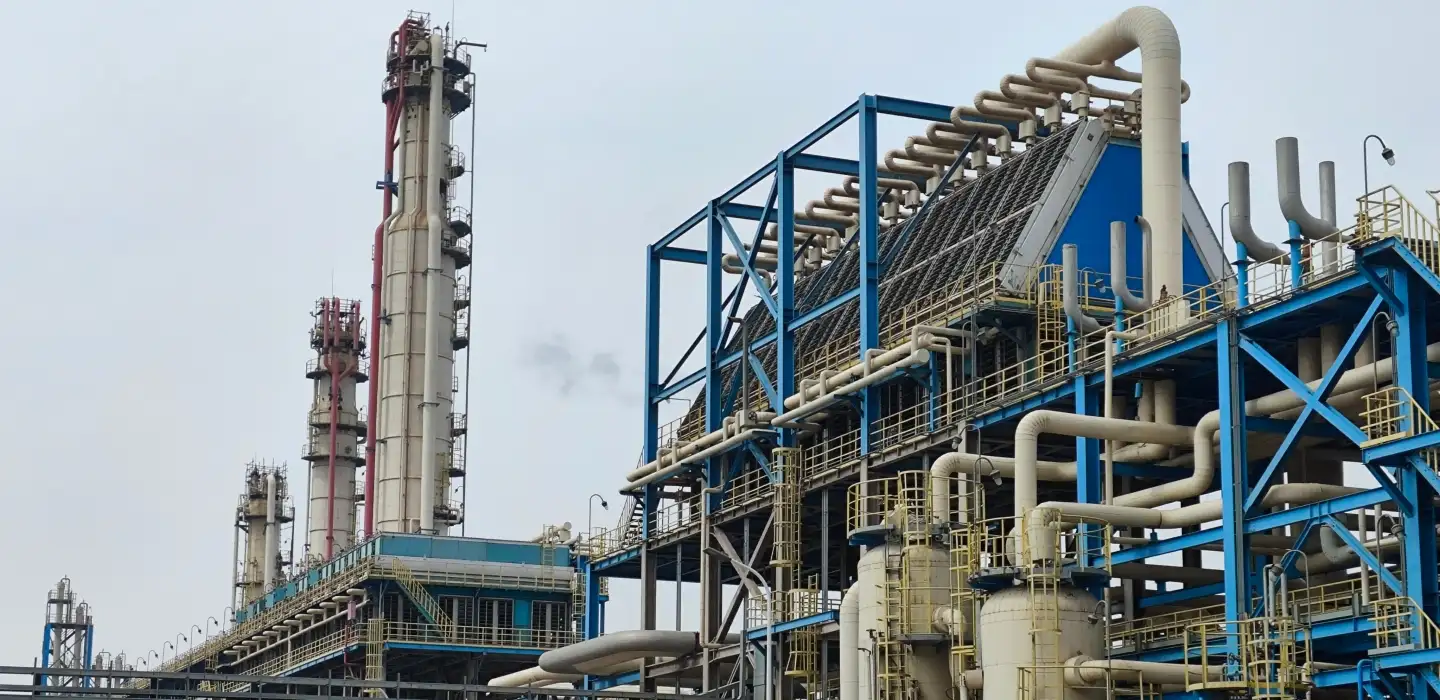
Hands on control and monitoring
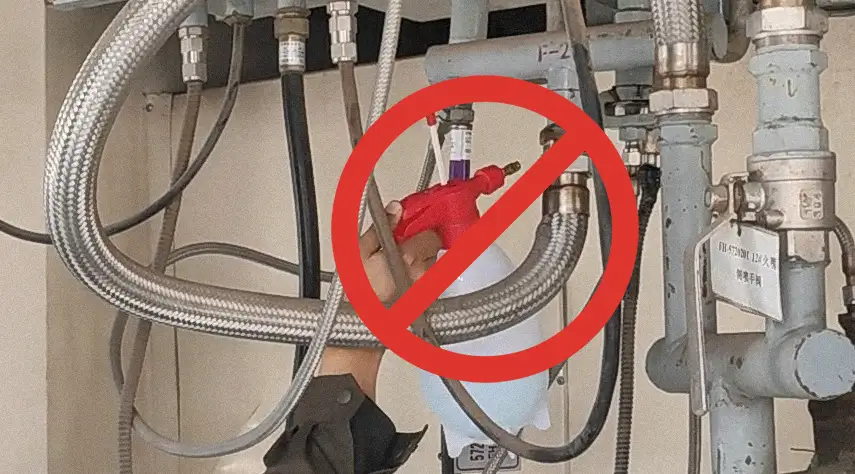
The gas concentration alarm relies on gas entering the device, which can be problematic in a negative pressure environment. This makes it challenging to detect negative pressure leaks using the soap bubble method. Additionally, infrared detectors can be influenced by temperature variations. As a result, these methods may fail to identify negative pressure leaks and can lead to inefficiencies.
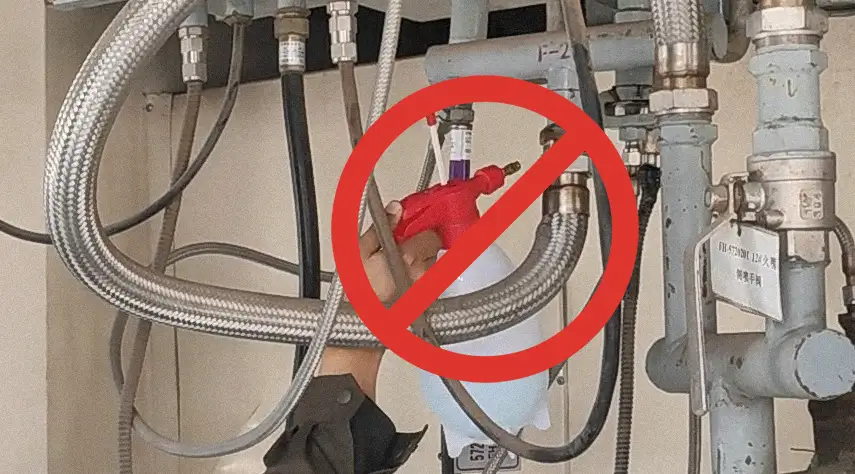
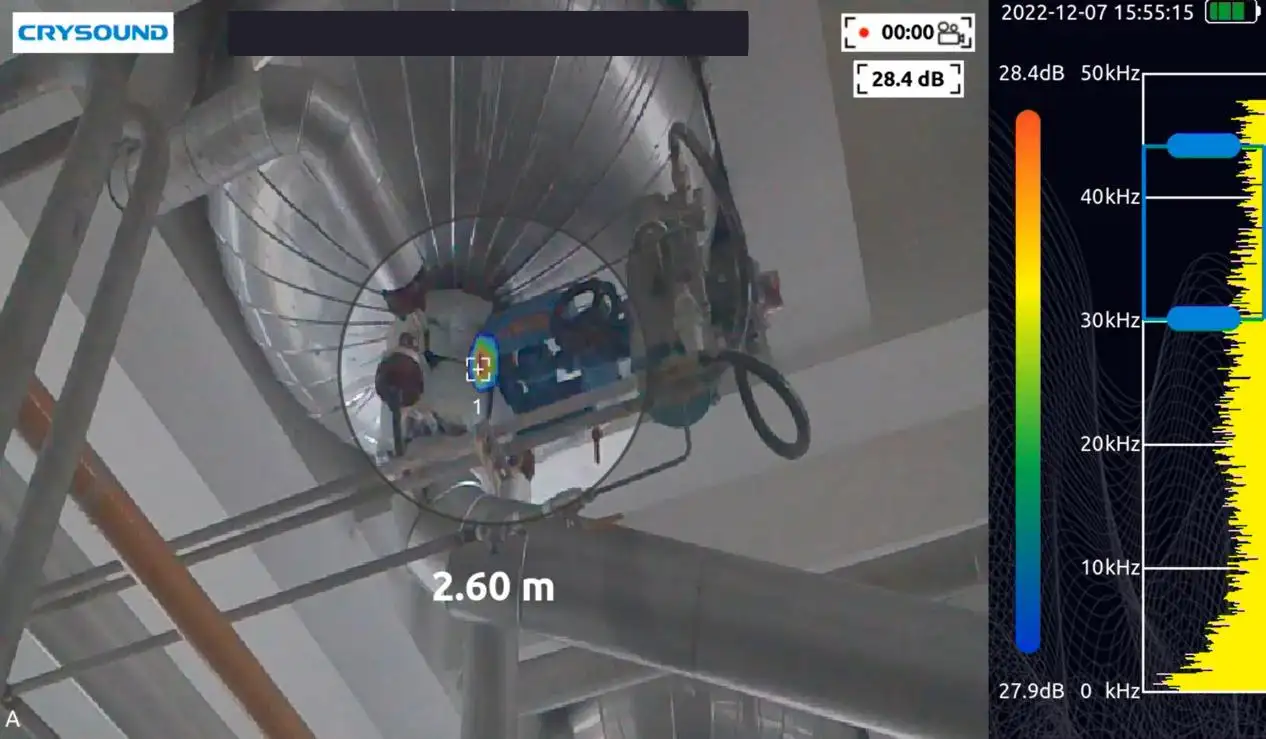
As an example, a chemical company has struggled for an extended period to achieve the necessary vacuum level, impacting its production capacity. The factory's current detection methods are inadequate, requiring the system to be filled with nitrogen to increase pressure before using soapy water to identify leaks. This approach is both time-consuming and labor-intensive, leading to substantial financial losses.
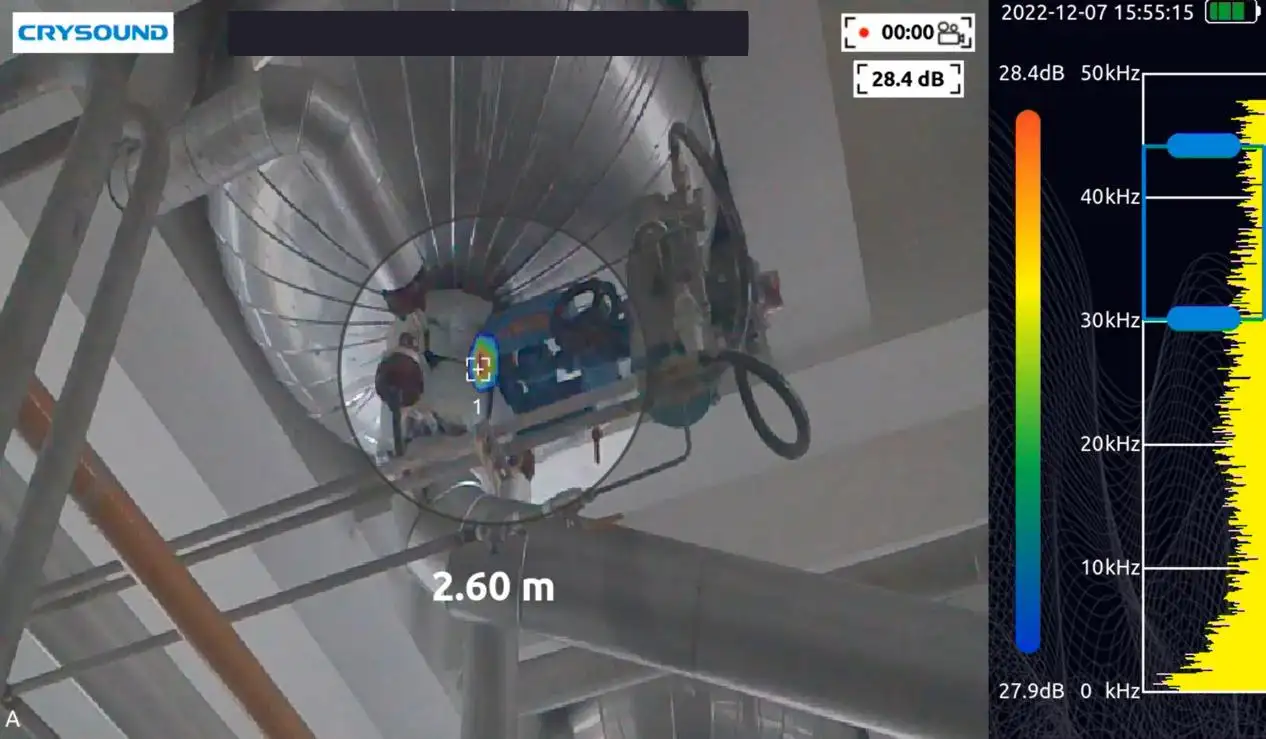
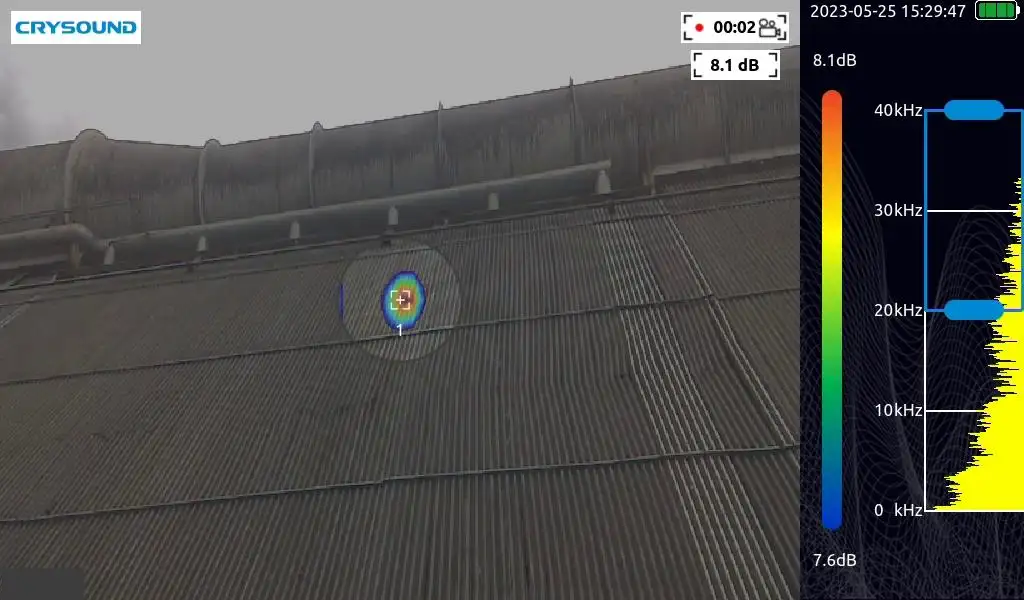
As an example, a coal chemical company’s air-cooling pipeline carries high-temperature gas (70°C) under negative pressure. The thin pipe walls and aging equipment make it prone to leaks. While personnel using ultrasonic listening devices can identify a general area of the leak, they must approach closely to pinpoint the exact location, creating a immediate safety concern.
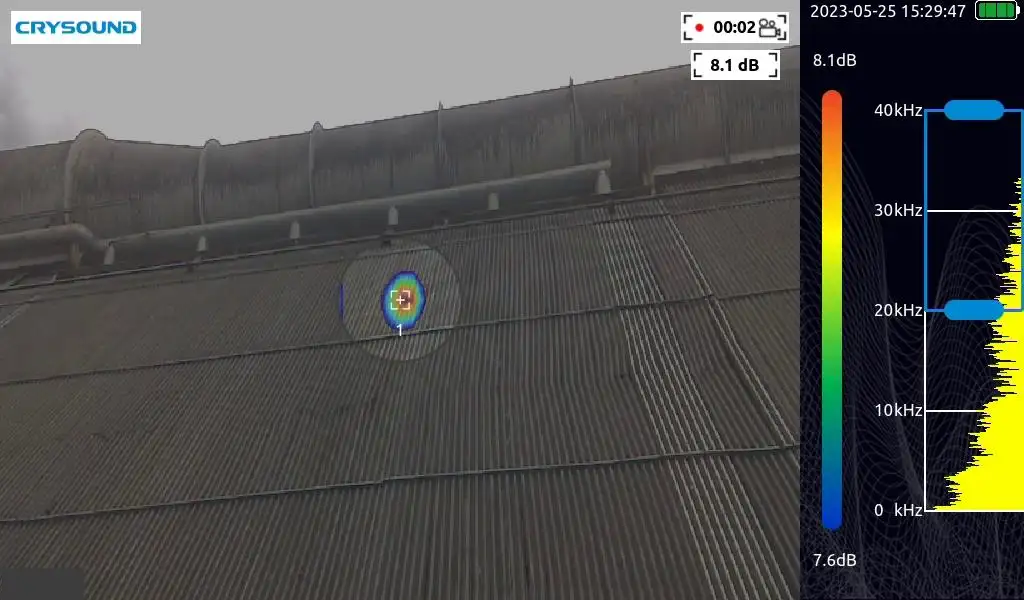
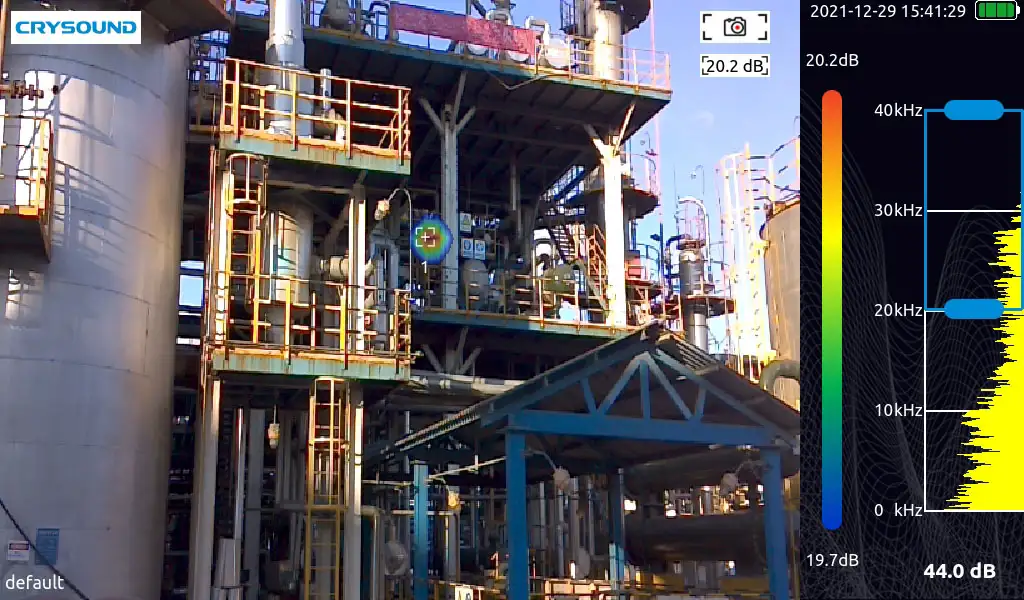
As an example, a photovoltaic manufacturing company is experiencing a sudden drop in airflow within its negative pressure pipelines, which is failing to meet production requirements. Compounding the issue, there are no effective methods for detecting vacuum leaks. The exhaust ducts are both high and complex, and personnel currently assess potential leaks by physically touching the pipes, which exposes them to the risk of burns.
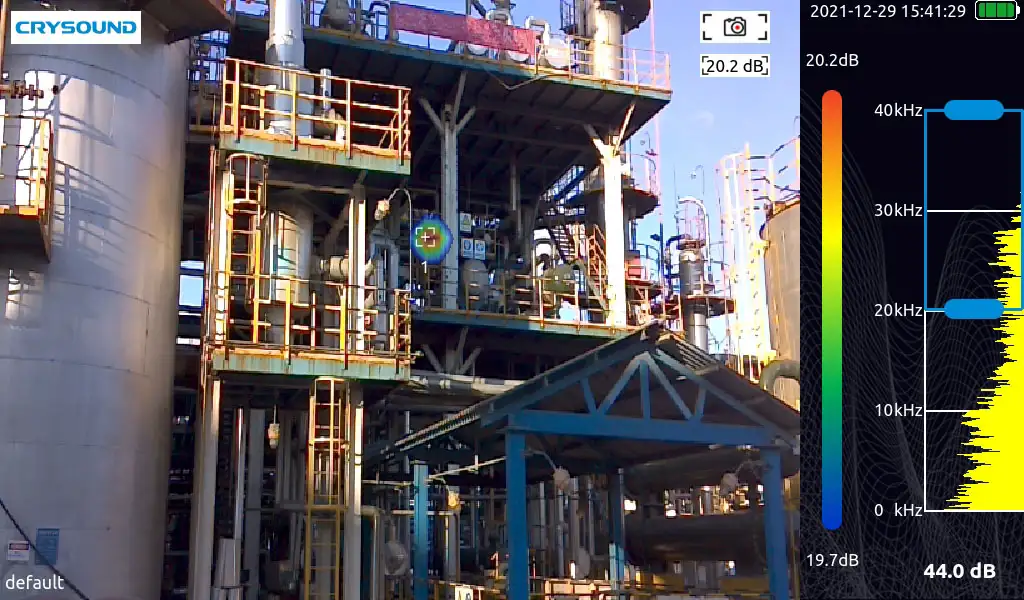
The gas concentration alarm relies on gas entering the device, which can be problematic in a negative pressure environment. This makes it challenging to detect negative pressure leaks using the soap bubble method. Additionally, infrared detectors can be influenced by temperature variations. As a result, these methods may fail to identify negative pressure leaks and can lead to inefficiencies.
The gas concentration alarm relies on gas entering the device, which can be problematic in a negative pressure environment. This makes it challenging to detect negative pressure leaks using the soap bubble method. Additionally, infrared detectors can be influenced by temperature variations. As a result, these methods may fail to identify negative pressure leaks and can lead to inefficiencies.
The gas concentration alarm relies on gas entering the device, which can be problematic in a negative pressure environment. This makes it challenging to detect negative pressure leaks using the soap bubble method. Additionally, infrared detectors can be influenced by temperature variations. As a result, these methods may fail to identify negative pressure leaks and can lead to inefficiencies.
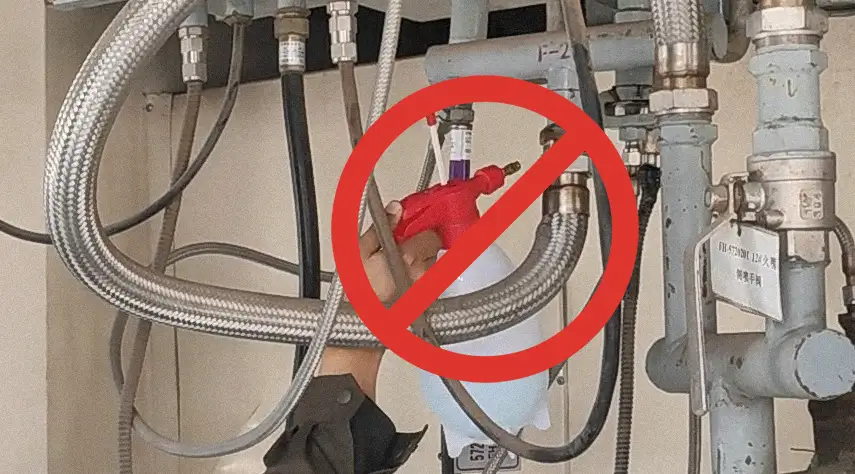
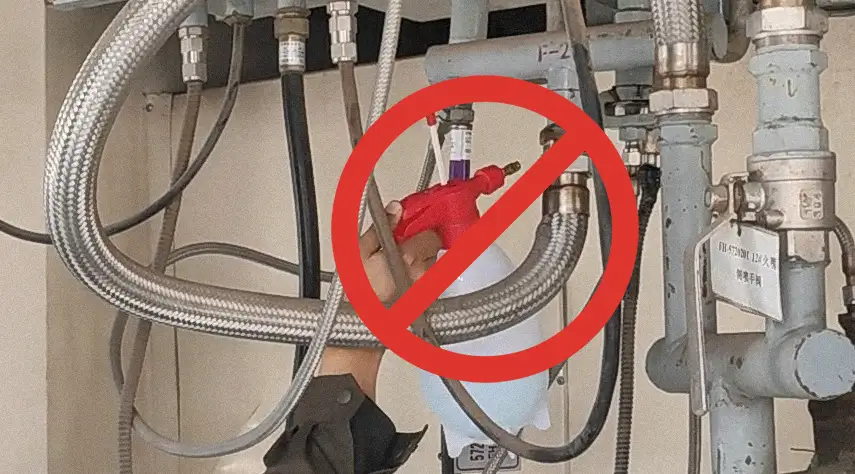
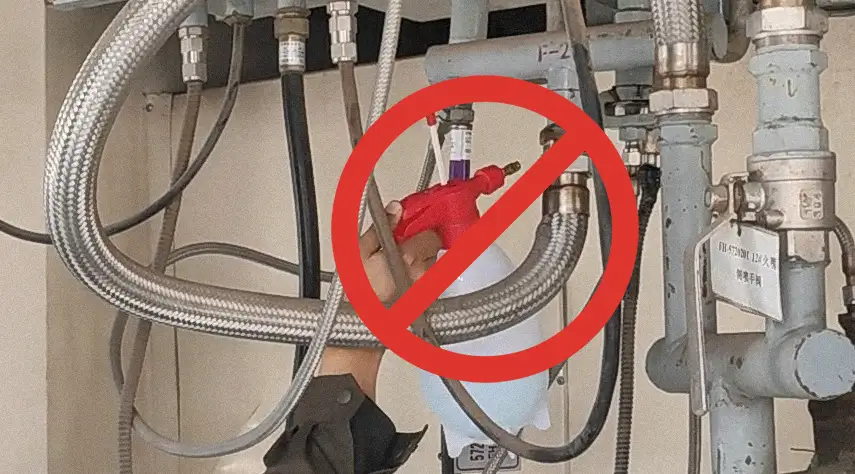
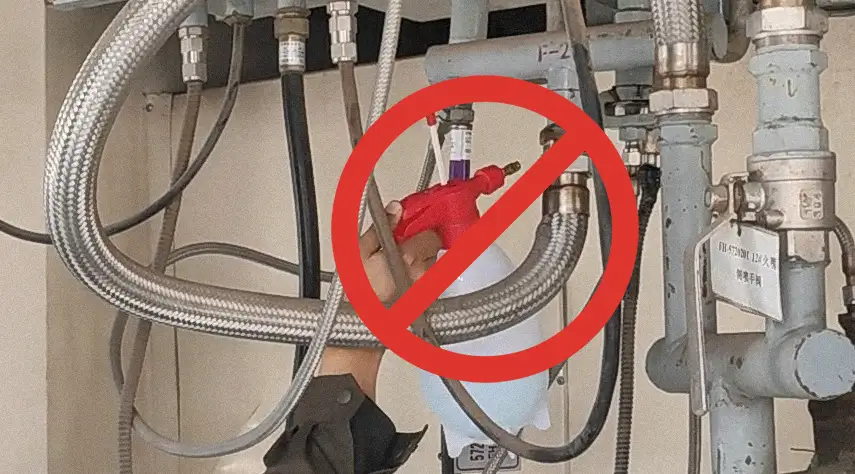
As an example, a chemical company has struggled for an extended period to achieve the necessary vacuum level, impacting its production capacity. The factory's current detection methods are inadequate, requiring the system to be filled with nitrogen to increase pressure before using soapy water to identify leaks. This approach is both time-consuming and labor-intensive, leading to substantial financial losses.
As an example, a chemical company has struggled for an extended period to achieve the necessary vacuum level, impacting its production capacity. The factory's current detection methods are inadequate, requiring the system to be filled with nitrogen to increase pressure before using soapy water to identify leaks. This approach is both time-consuming and labor-intensive, leading to substantial financial losses.
As an example, a chemical company has struggled for an extended period to achieve the necessary vacuum level, impacting its production capacity. The factory's current detection methods are inadequate, requiring the system to be filled with nitrogen to increase pressure before using soapy water to identify leaks. This approach is both time-consuming and labor-intensive, leading to substantial financial losses.
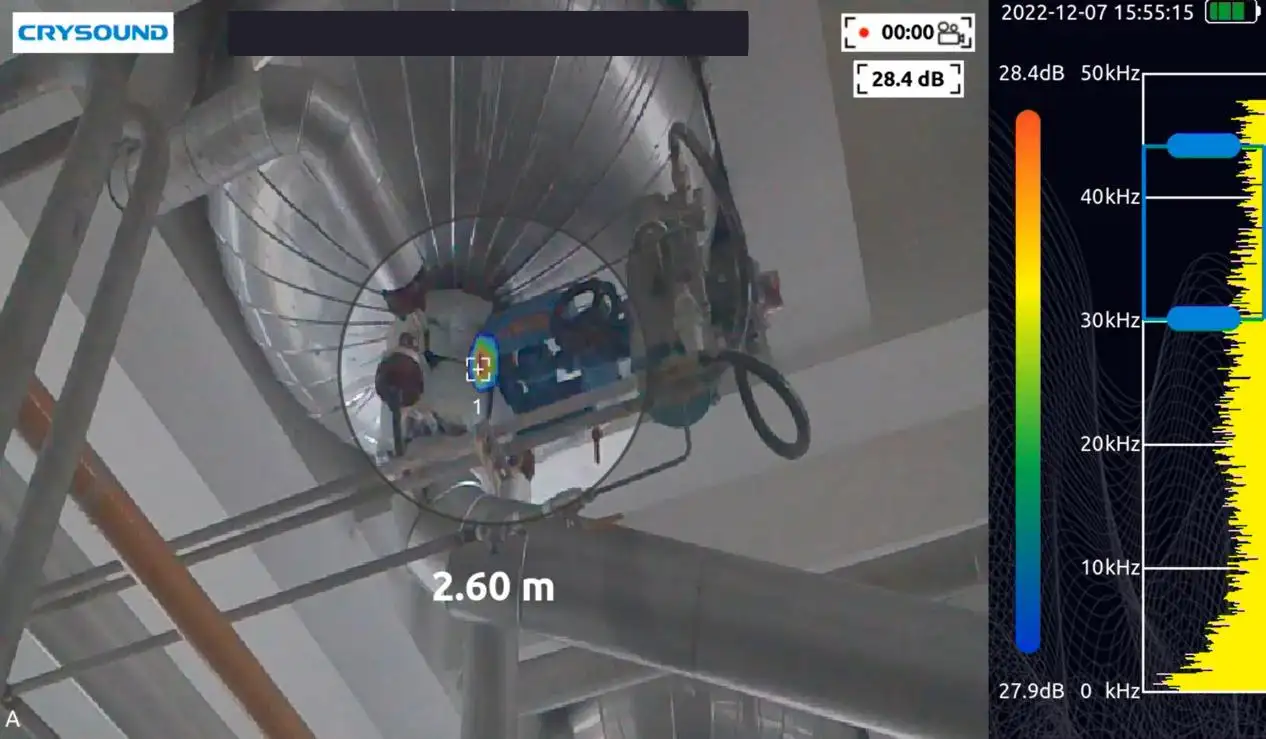
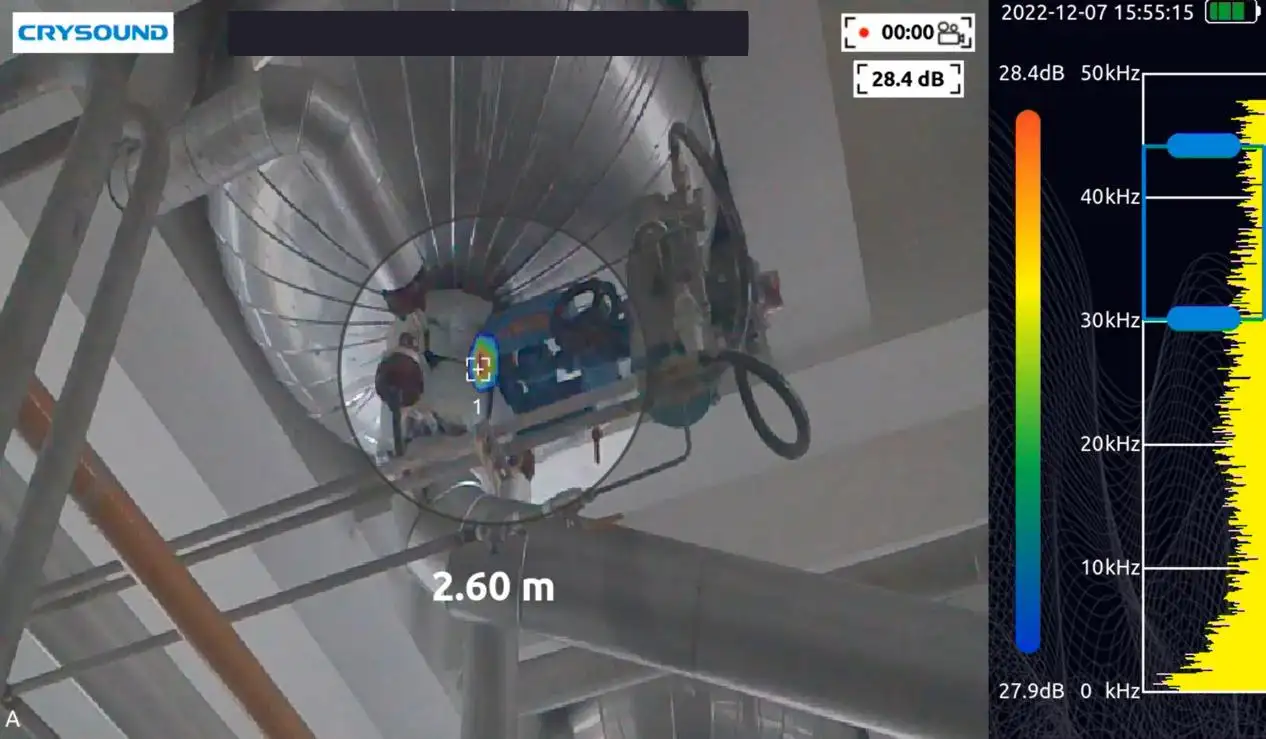
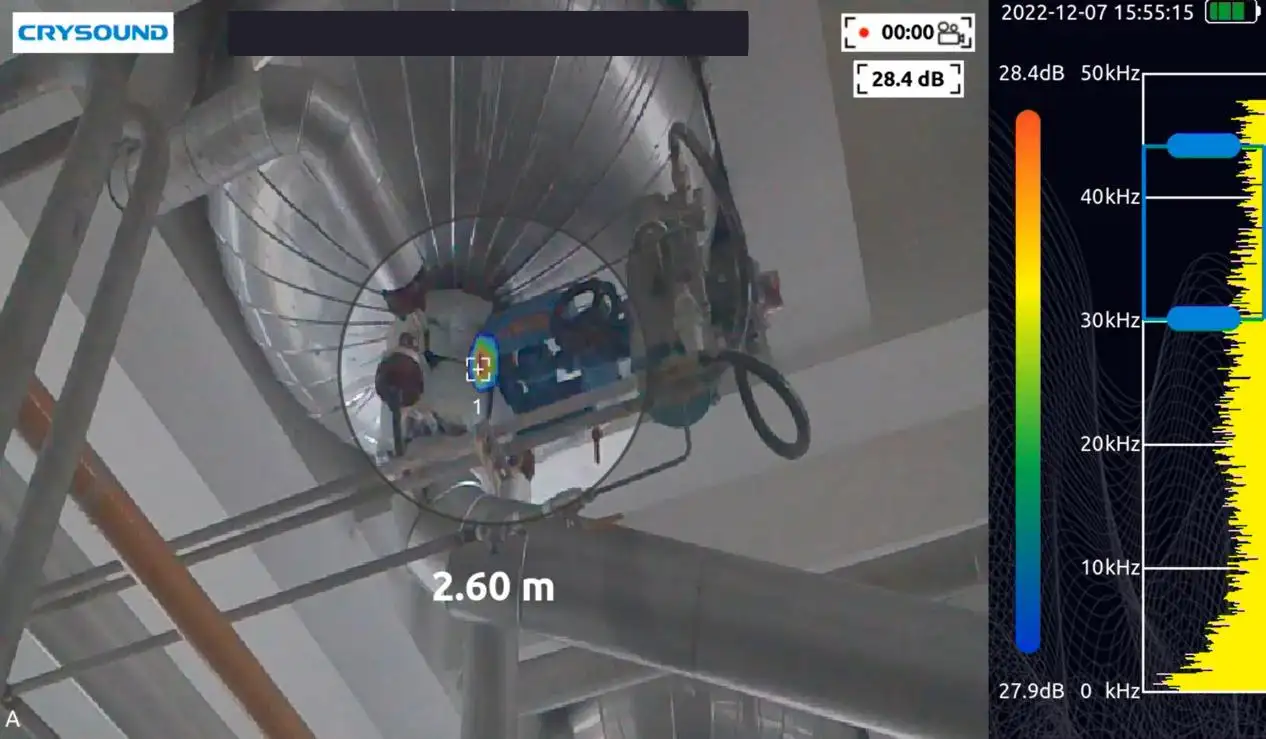
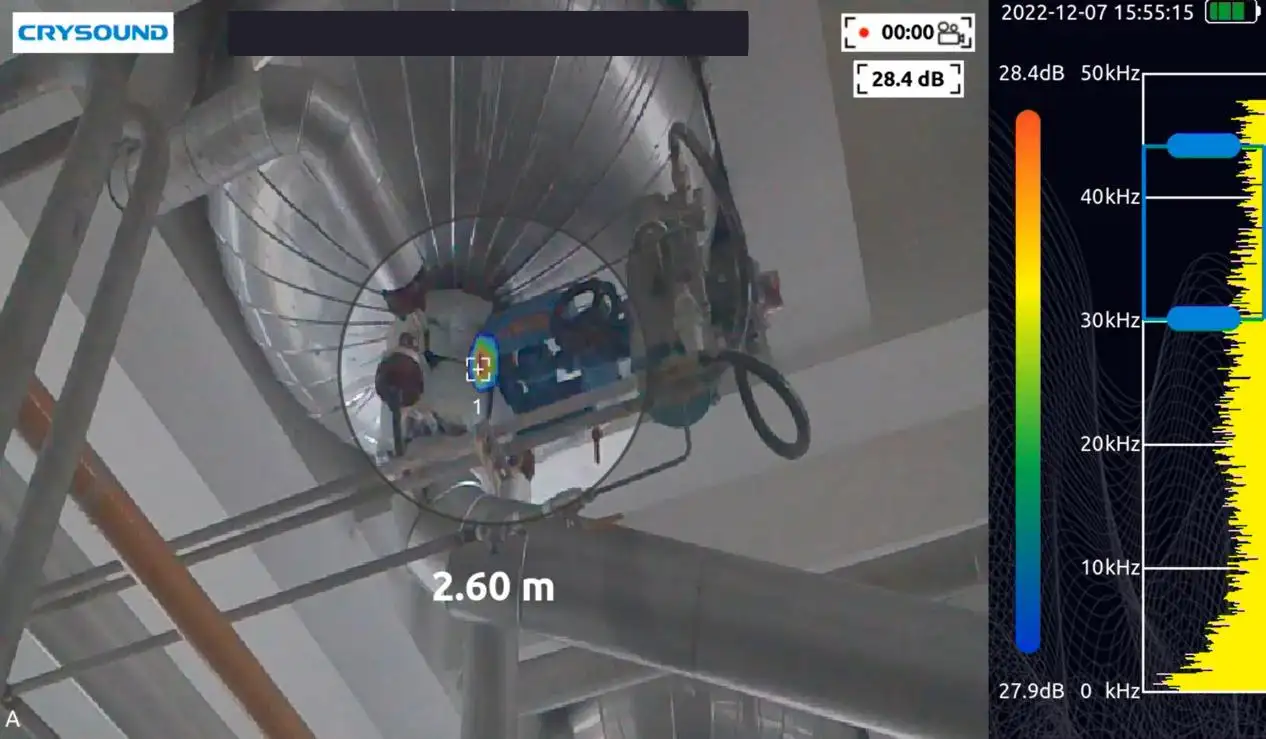
As an example, a coal chemical company’s air-cooling pipeline carries high-temperature gas (70°C) under negative pressure. The thin pipe walls and aging equipment make it prone to leaks. While personnel using ultrasonic listening devices can identify a general area of the leak, they must approach closely to pinpoint the exact location, creating a immediate safety concern.
As an example, a coal chemical company’s air-cooling pipeline carries high-temperature gas (70°C) under negative pressure. The thin pipe walls and aging equipment make it prone to leaks. While personnel using ultrasonic listening devices can identify a general area of the leak, they must approach closely to pinpoint the exact location, creating a immediate safety concern.
As an example, a coal chemical company’s air-cooling pipeline carries high-temperature gas (70°C) under negative pressure. The thin pipe walls and aging equipment make it prone to leaks. While personnel using ultrasonic listening devices can identify a general area of the leak, they must approach closely to pinpoint the exact location, creating a immediate safety concern.
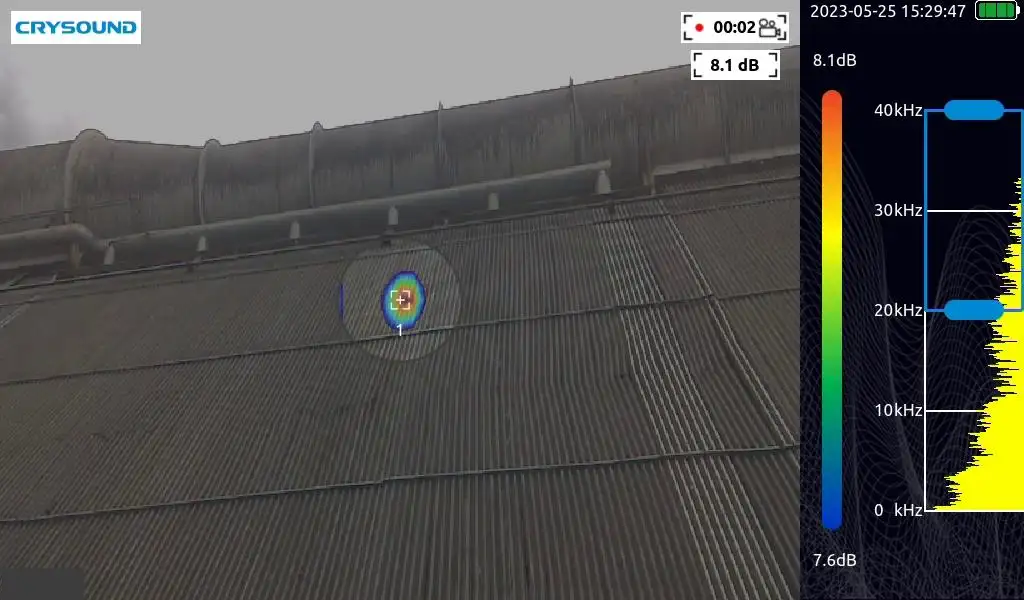
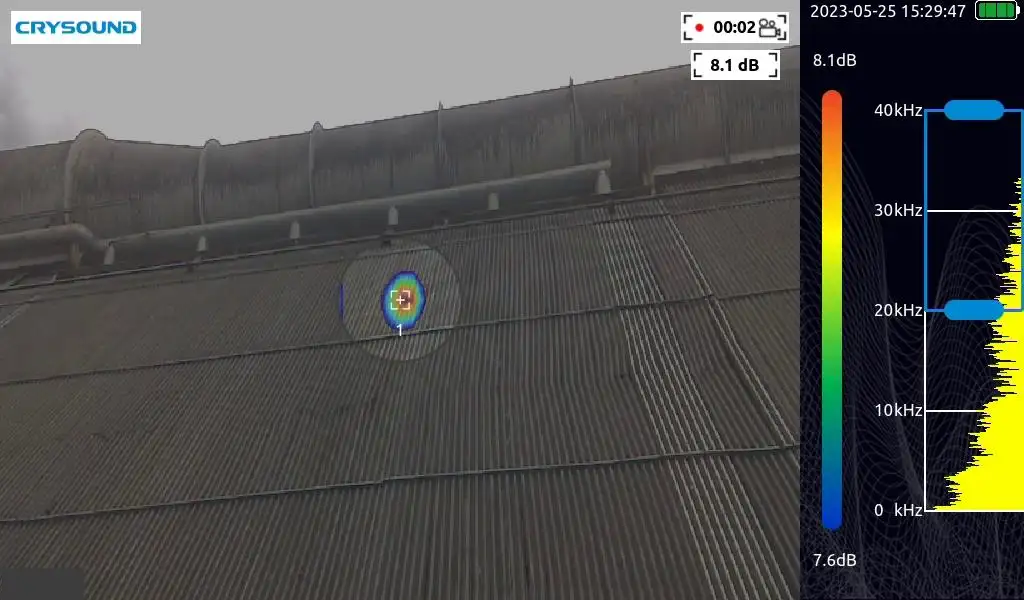
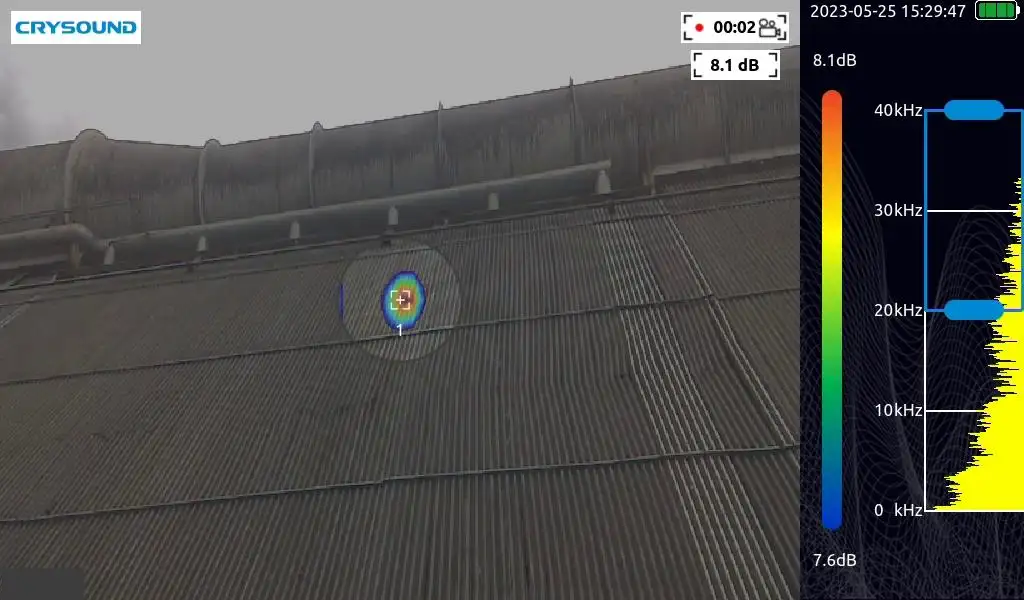
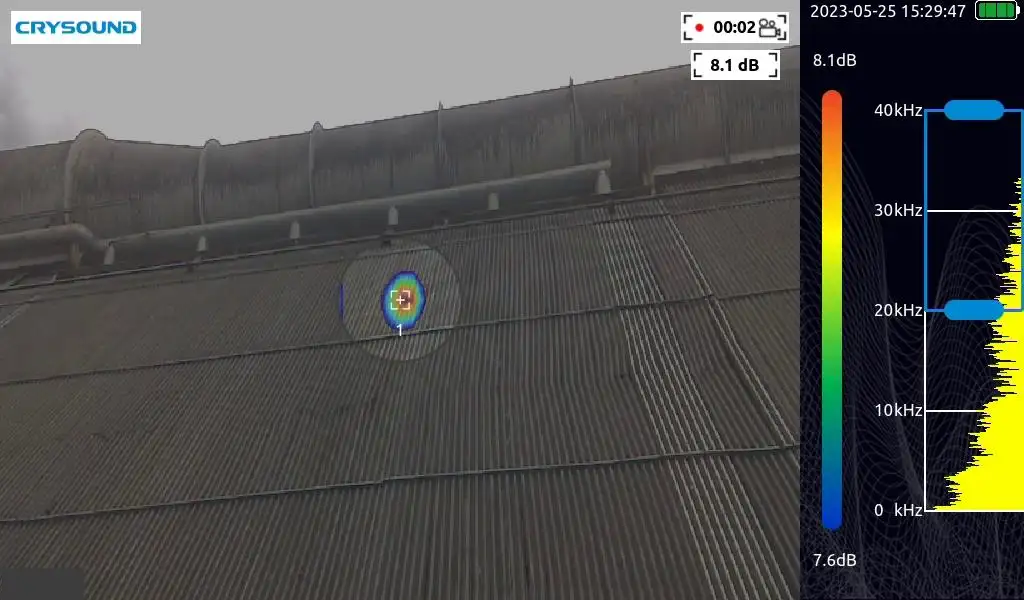
As an example, a photovoltaic manufacturing company is experiencing a sudden drop in airflow within its negative pressure pipelines, which is failing to meet production requirements. Compounding the issue, there are no effective methods for detecting vacuum leaks. The exhaust ducts are both high and complex, and personnel currently assess potential leaks by physically touching the pipes, which exposes them to the risk of burns.
As an example, a photovoltaic manufacturing company is experiencing a sudden drop in airflow within its negative pressure pipelines, which is failing to meet production requirements. Compounding the issue, there are no effective methods for detecting vacuum leaks. The exhaust ducts are both high and complex, and personnel currently assess potential leaks by physically touching the pipes, which exposes them to the risk of burns.
As an example, a photovoltaic manufacturing company is experiencing a sudden drop in airflow within its negative pressure pipelines, which is failing to meet production requirements. Compounding the issue, there are no effective methods for detecting vacuum leaks. The exhaust ducts are both high and complex, and personnel currently assess potential leaks by physically touching the pipes, which exposes them to the risk of burns.
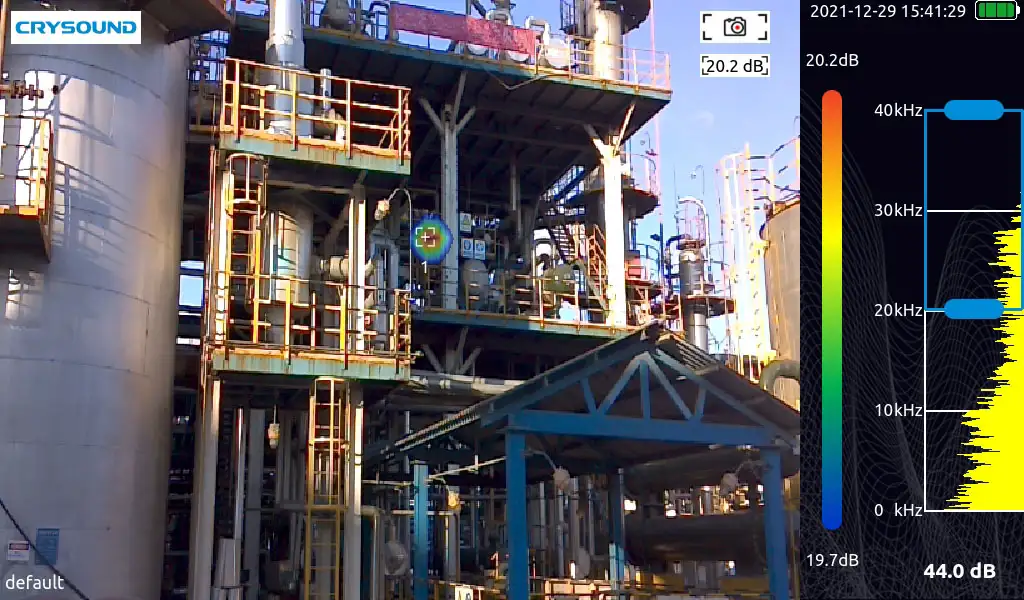
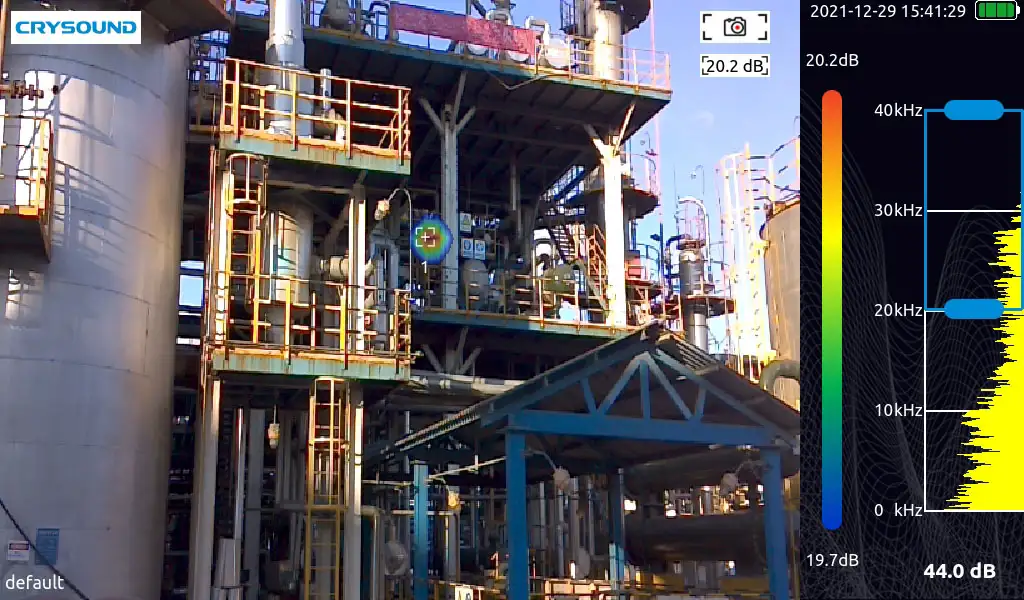
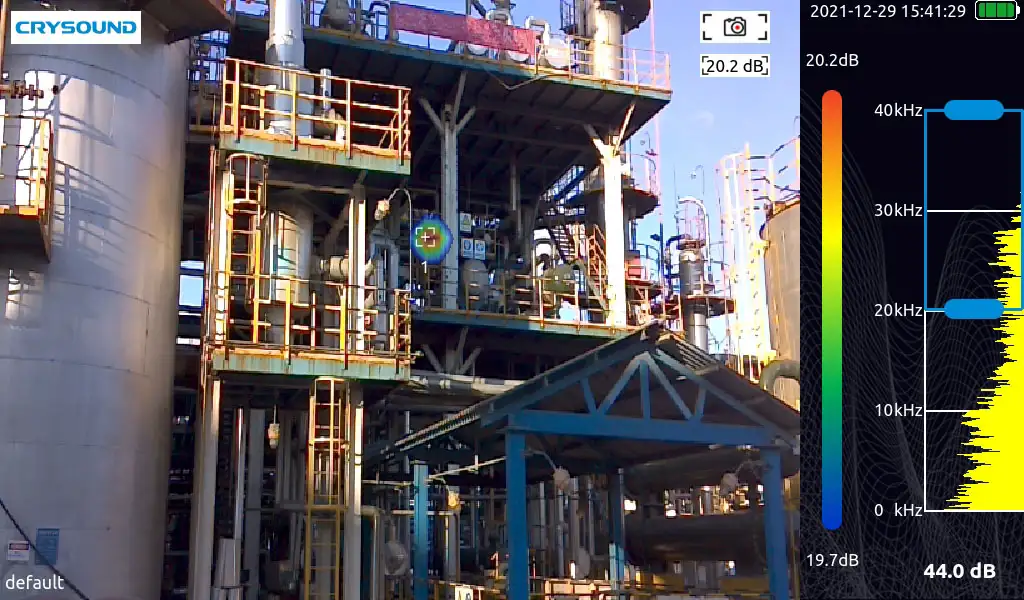
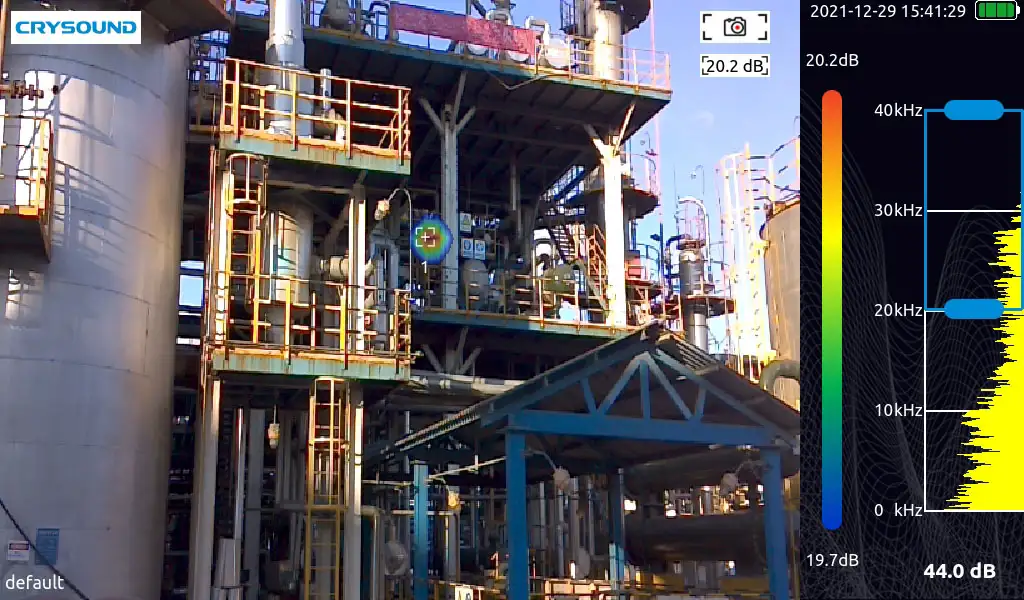
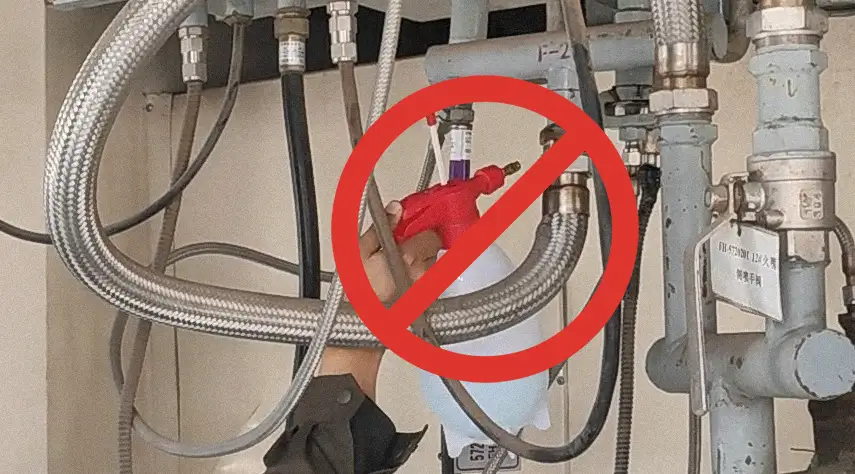
The gas concentration alarm relies on gas entering the device, which can be problematic in a negative pressure environment. This makes it challenging to detect negative pressure leaks using the soap bubble method. Additionally, infrared detectors can be influenced by temperature variations. As a result, these methods may fail to identify negative pressure leaks and can lead to inefficiencies.
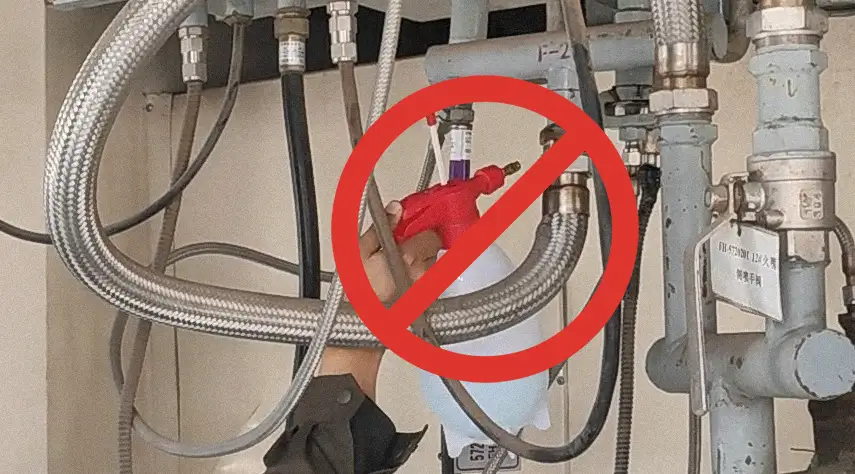
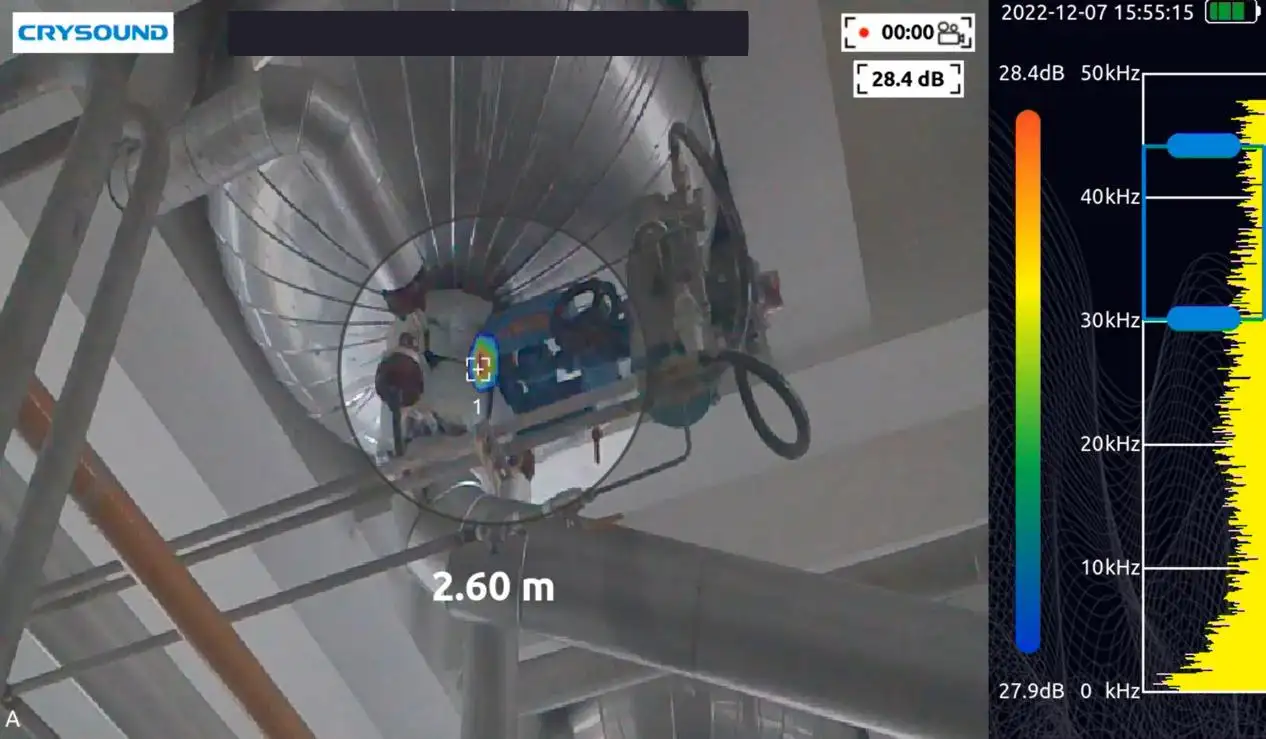
As an example, a chemical company has struggled for an extended period to achieve the necessary vacuum level, impacting its production capacity. The factory's current detection methods are inadequate, requiring the system to be filled with nitrogen to increase pressure before using soapy water to identify leaks. This approach is both time-consuming and labor-intensive, leading to substantial financial losses.
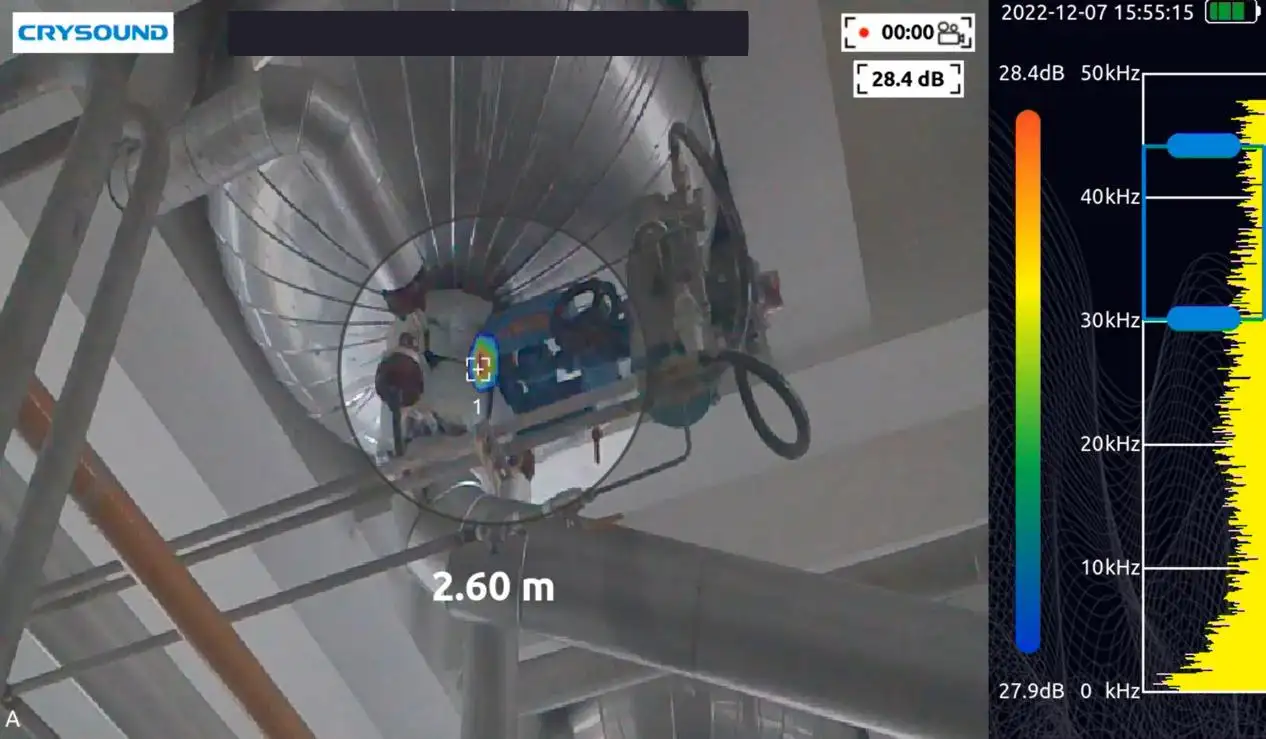
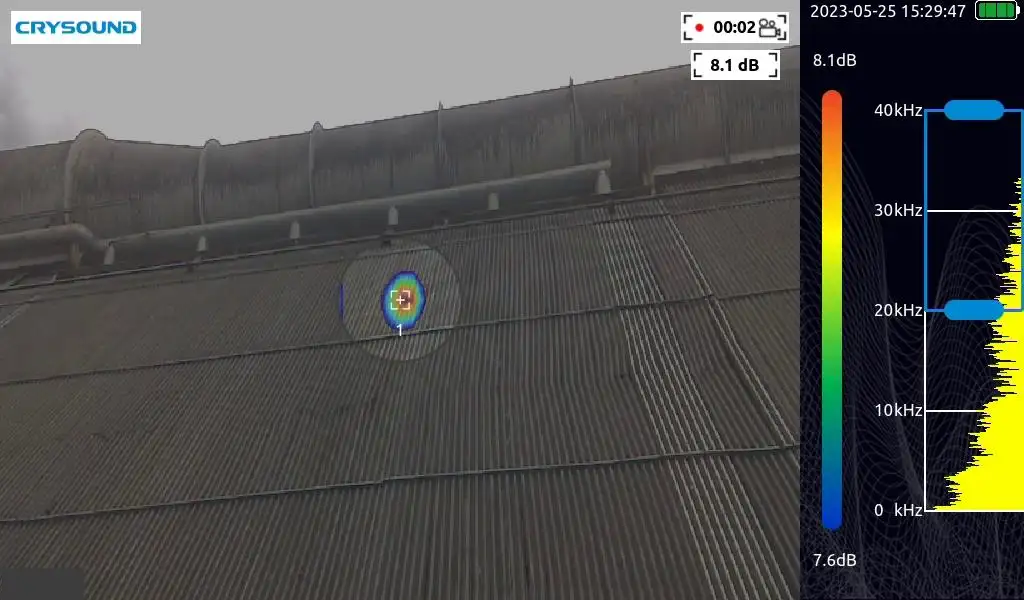
As an example, a coal chemical company’s air-cooling pipeline carries high-temperature gas (70°C) under negative pressure. The thin pipe walls and aging equipment make it prone to leaks. While personnel using ultrasonic listening devices can identify a general area of the leak, they must approach closely to pinpoint the exact location, creating a immediate safety concern.
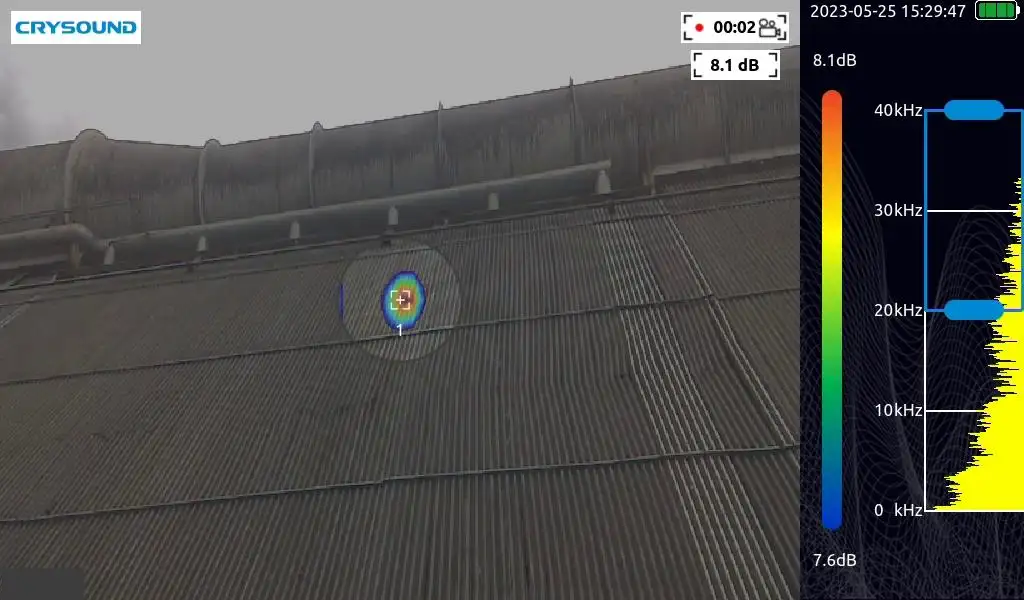
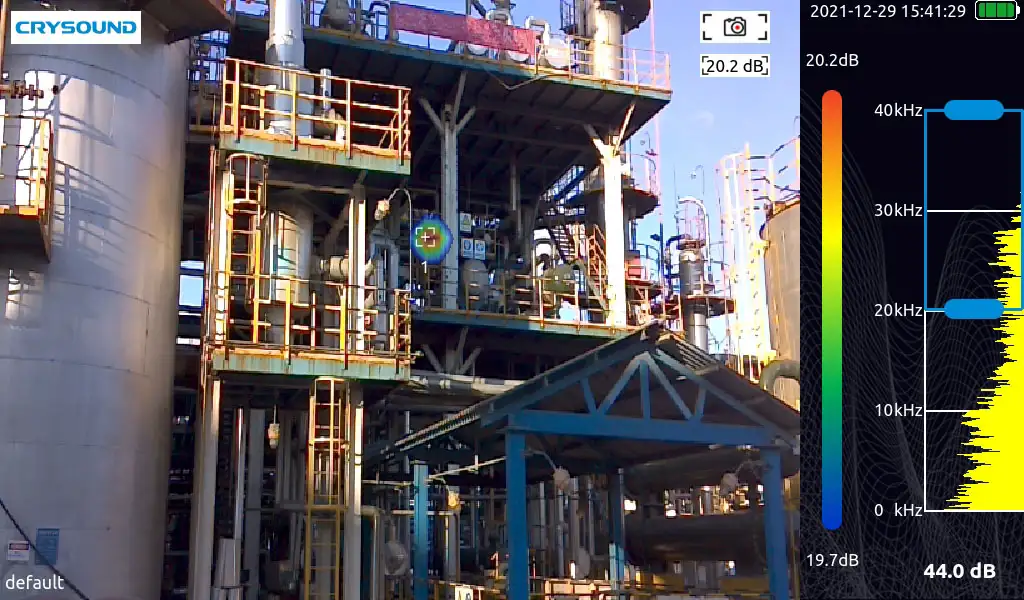
As an example, a photovoltaic manufacturing company is experiencing a sudden drop in airflow within its negative pressure pipelines, which is failing to meet production requirements. Compounding the issue, there are no effective methods for detecting vacuum leaks. The exhaust ducts are both high and complex, and personnel currently assess potential leaks by physically touching the pipes, which exposes them to the risk of burns.
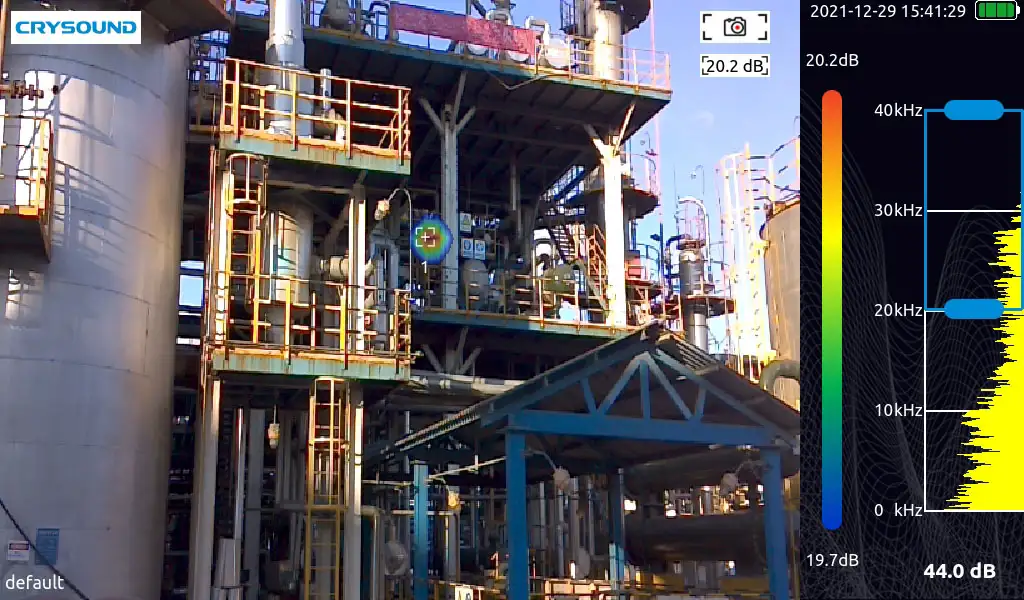
System Devices
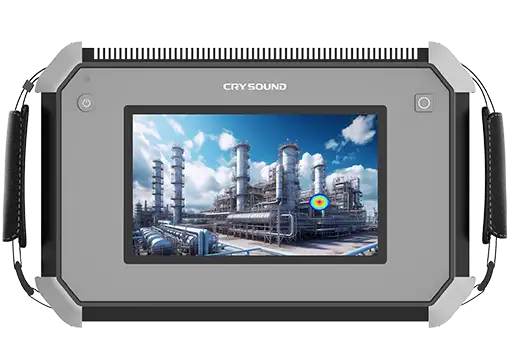
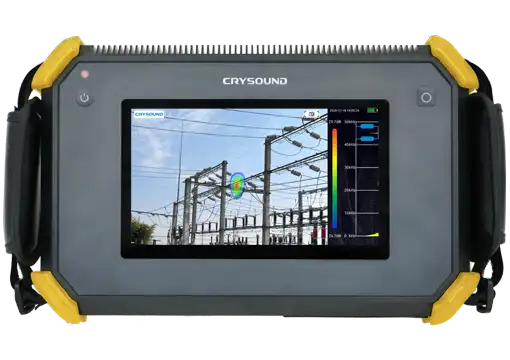
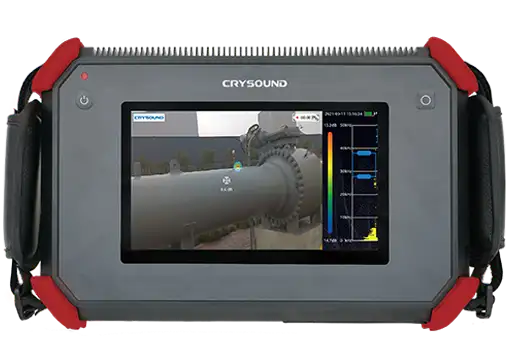
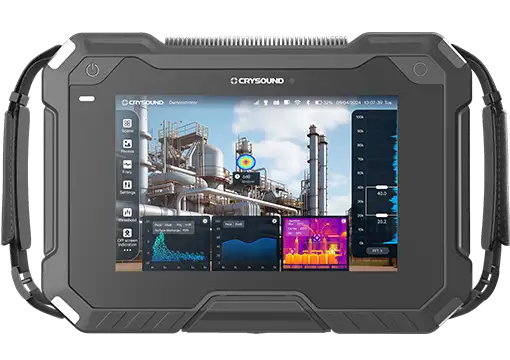
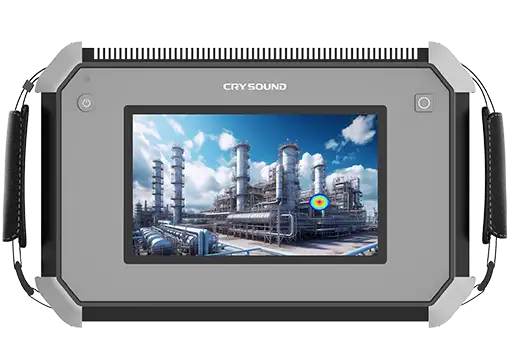
The CRY2620 Industrial Acoustic Imaging Camera is designed for ease of use and quick operation. Its robust aluminum alloy shell ensures durability, making it adaptable to complex and changing work environments. The device provides a real-time sound image display, significantly accelerating the detection of pressurized or vacuum leaks compared to traditional methods.
The CRY2620 simplifies testing with just two adjustable parameters: test frequency range and dynamic range, covering most testing needs.
It offers multiple modes, including camera and video modes, along with flexible on-site data recording. The large-capacity TF storage card is expandable, allowing for quick export and reporting of test results.
This device helps enterprises minimize losses from gas leaks and other accidents, enhancing overall operational safety.
.png)

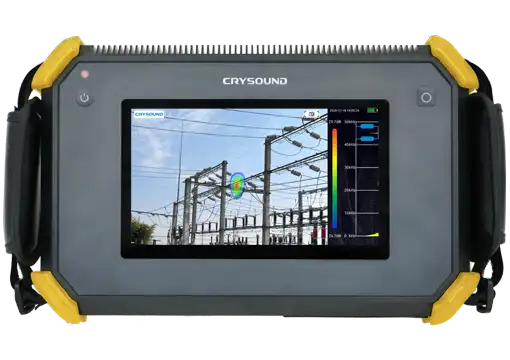
The CRY2623 is a 128-mic industrial acoustic imaging camera that is user-friendly and requires minimal training. Its durable aluminum alloy shell is built to withstand complex and variable working conditions. The device offers real-time acoustic imaging, significantly accelerating the detection of pressurized or vacuum leaks compared to traditional methods. It supports both photo and video modes for flexible on-site data recording. With an expandable large-capacity TF storage card, test results can be quickly exported and reported. The CRY2623 helps enterprises reduce safety risks and minimize economic losses associated with gas leaks, partial discharges, and other malfunctions.
.png)

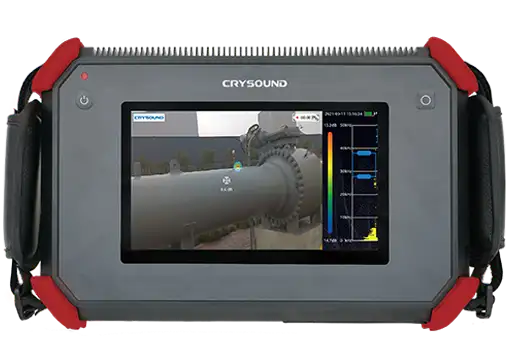
The CRY2624 is a 128-mic industrial acoustic imaging camera and is designed for use in explosive environments within the chemical and energy industries. Featuring a robust aluminum alloy shell, this device is built to withstand complex and dynamic work conditions. It offers real-time sound image display, significantly improving the speed of detecting pressurized or vacuum leaks compared to other methods.
The CRY2624 is ATEX certified with a rating of II 3G Ex ic IIC T5 Gc, ensuring safe operation in potentially explosive atmospheres while adhering to stringent safety standards. The device supports camera and video modes, providing flexible on-site data recording. With an expandable large-capacity TF storage card, test results can be quickly exported and reported. This camera helps industrial facilities minimize losses from gas leaks, partial discharge, and other accidents, enhancing overall safety and operational efficiency.
.png)

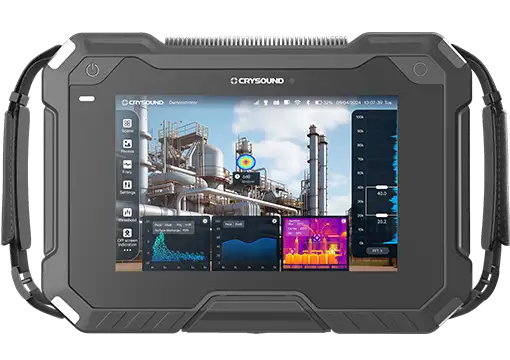
Introducing CRYSOUND’s cutting-edge acoustic imaging camera, revolutionizing industrial inspections with advanced capabilities. The CRY8124 acoustic imaging camera excels at pinpointing leaks, identifying electrical partial discharge, and detecting mechanical deterioration. Setting a new standard for sensitivity and efficiency, the CRY8124 boasts 200 microphones (the most in the industry). The device detects smaller leaks and partial discharges from greater distance than any other handheld acoustic imaging camera on the market.
The CRY8124 reporting software allows offline analysis, editing, and report generation, simplifying regular maintenance routines.
Elevate the effectiveness of your industrial inspections with CRYSOUND’s acoustic cameras.
.png)
